The MBO Group guarantees quick availability and high quality of spare and wear parts
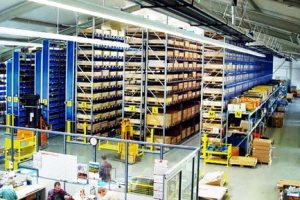
Around 19,500 different parts are stored at the Oppenweiler site, ensuring a quick supply of MBO spare and wear parts.
Oppenweiler, 26 May 2020 – An MBO combi folding machine consists of 6,400 individual parts on average. This number can even reach 9,000 parts for an MBO buckle folding machine. MBO folding machines are manufactured and assembled in accordance with strict quality requirements and are designed for constant 24/7 operation. However, individual parts of the machines can still break from time to time or may need to be replaced as part of maintenance or servicing work. In such cases, it is easiest to obtain the required parts directly from the manufacturer.
Independent supply chains through a dedicated production facility
The MBO Group has its own production facility in Portugal. Here, around 80 per cent of the parts installed in MBO folding machines are manufactured by the company itself, making it largely independent when it comes to global supply chains and shortages. Another advantage is that the high quality standards of the MBO Group are applied as early as the manufacturing phase. The MBO Portugal production site houses a CNC machining centre, a galvanizing installation and a painting line, amongst other things.
Once the spare and wear parts have been manufactured in Portugal, most of them end up in the logistics centre of the MBO Group in Oppenweiler, near Stuttgart, where the company’s headquarters are also located. Around 19,500 different parts are stored here at any one time – not just for the latest models, but also for older MBO folding machines. Of these, approximately 3,000 spare and wear parts in total fill the numerous shelves. This high level of availability ensures that the components required are received quickly by the end customers.
The parts can be ordered from MBO either “traditionally” on the phone or by email. Alternatively, there is an order form on MBO’s website and an online shop is also due to launch soon.
Sustainably packaged to protect the environment
The MBO Group operates worldwide. It has branches on three continents and an international network of independent sales partners in over 60 countries. In this context, the Group is extremely conscious of its responsibility and its role in setting a good example in the field of sustainability to protect nature. Special emphasis is placed on reusable and recyclable packaging. For example, MBO foldrollers are delivered in sturdy cardboard boxes that can be used multiple times. The boxes are made entirely of cardboard without metal clips and are therefore really easy to recycle. To additionally protect the foldrollers in transit, they are wrapped in nets of strong paper. Instead of polystyrene, scrunched-up paper is used as padding material in the spare parts packages. Last but not least, the packages are sealed with tape made of potato starch.
The MBO Group provides comprehensive services
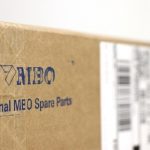
The MBO Group opts for sustainable packaging to protect the environment.
The MBO Group offers a wide range of services. Rapid and uncomplicated support can be given far and wide on the phone or via the remote maintenance tool RAS. MBO’s technicians also deal with the installation work for spare and wear parts or take care of the maintenance, servicing or relocation of folding machines. What’s more, the MBO Group has various maintenance contracts available, for example the so-called “Care Check” for the stacking robot CoBo-Stack, which is carried out twice a year, or the annual “Care Check” for the log stacker A10.
Customers of the MBO Group can also be sure that they will receive great all-round aftercare when they purchase an MBO folding machine – either directly through the MBO customer centre or from trained personnel at over 60 global, independent sales agencies.
More information on the MBO Group is available here: https://www.mboamerica.com/.